Comment est fabriquée la RAM ?
Vous êtes vous déjà demandé de quoi est faite la mémoire et comment elle est fabriquée ? Nous vous emmenons en coulisses afin que vous puissiez découvrir les processus mis en place pour fabriquer la mémoire et pour vérifier que vous obtenez un produit de haute qualité.
Il existe trois types de mémoire différents, mais ils sont tous fabriqués de la même manière. Cliquez ici pour découvrir les caractéristiques de chacun des trois types de mémoire. Pour plus d’informations sur les différents types de mémoire serveur, cliquez ici.
Partie I : Du silicium au wafer fini
Les puces de mémoire sont composées de circuits intégrés comportant plusieurs transistors, résistances et condensateurs qui doivent être formés sur chaque puce. Ces circuits intégrés commencent leur cycle de vie sous forme de silicium, généralement extrait du sable. Transformer le silicium en puces de mémoire est un processus extrêmement méticuleux qui nécessite l’expertise d’ingénieurs, de métallurgistes, de chimistes et de physiciens. La mémoire est dans une grande usine, appelée « fab », qui comporte de nombreuses salles blanches. Les puces de mémoire en semi-conducteurs sont fabriquées dans des salles blanches, car les circuits imprimés sont si petits que le moindre grain de poussière peut les endommager. Le principal site de Micron, à Boise, Idaho, aux États-Unis, s’étend sur plus de 165 000 m² et dispose de salles blanches de classe 1 et de classe 10. Dans les salles blanches de classe 1, il n’y a pas plus de 35 particules de poussière par mètre cube d’air. En comparaison, une chambre propre dans un hôpital moderne compte environ 350 000 particules de poussière par mètre cube d’air. L’air de la pièce est filtré et circule en permanence. Les membres des équipes de production portent des charlottes, des combinaisons et des masques spéciaux qui leur permettent de ne pas polluer l’air avec des particules.
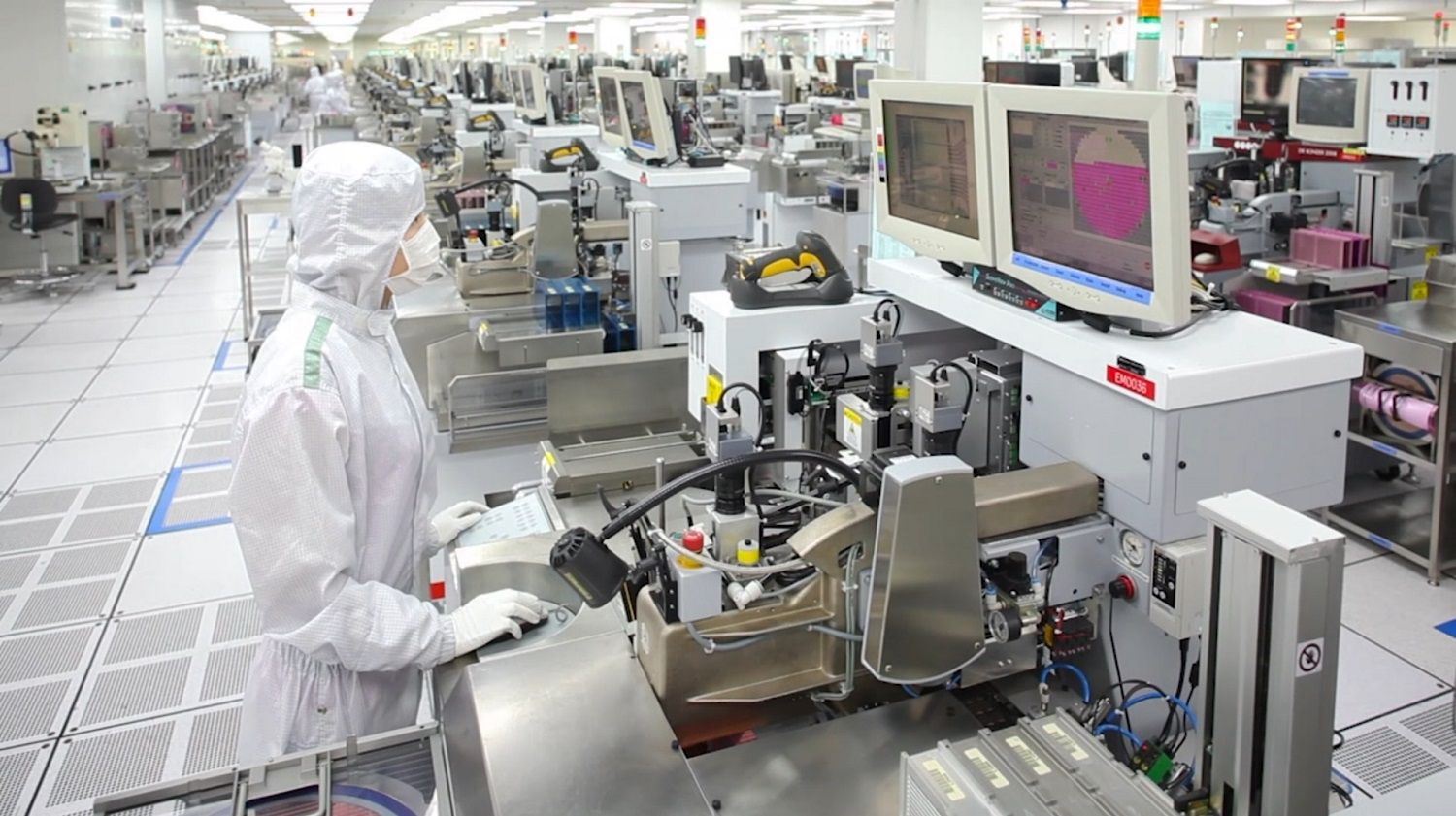
Étape 1 : Les lingots de silicium
La première étape de la transformation du silicium en circuit intégré est la création d’un cylindre (ou lingot) pur, monocristallin, composé de silicium et mesurant 330 mm de diamètre. Une fois formés, les lingots de silicium sont découpés en fines tranches (wafer) de moins de 6 mm d’épaisseur, qui sont ensuite polies. Les éléments du circuit de la puce (transistors, résistances, condensateurs) sont ensuite construits par couche sur le wafer de silicium. Les circuits sont développés et testés par simulation, puis perfectionnés sur ordinateur avant d’être fabriqués. Une fois la conception complète, un masque photographique en verre est fabriqué pour chaque couche du circuit. Les masques photographiques sont des gabarits dotés de zones évidées et de zones opaques, laissant passer la lumière selon un motif précis. Ils sont essentiels pour l’étape suivante du processus de fabrication : la photolithographie.
Étape 2 : La photolithographie
Dans une salle blanche stérile, les wafers subissent un processus de photolithographie en plusieurs étapes, qui sera répété pour chaque masque requis par le circuit. Les masques sont utilisés (a) pour définir les différents éléments d’un transistor, d’une résistance, d’un condensateur ou d’un connecteur qui viendra compléter le circuit électrique, et (b) pour définir le motif du circuit sur chaque couche constituant le composant. Au début du processus de production, les wafers de silicium nu sont recouverts d’une fine couche de verre, puis d’une épaisseur de nitrure. La couche de verre est formée en exposant le wafer en silicium à de l’oxygène chauffé à 900 °C pendant au moins une heure, la durée dépendant de l’épaisseur de la couche souhaitée. Le verre (dioxyde de silicium) est formé en exposant le silicium du wafer à de l’oxygène. À haute température, la réaction chimique (appelée « oxydation ») a lieu très rapidement.
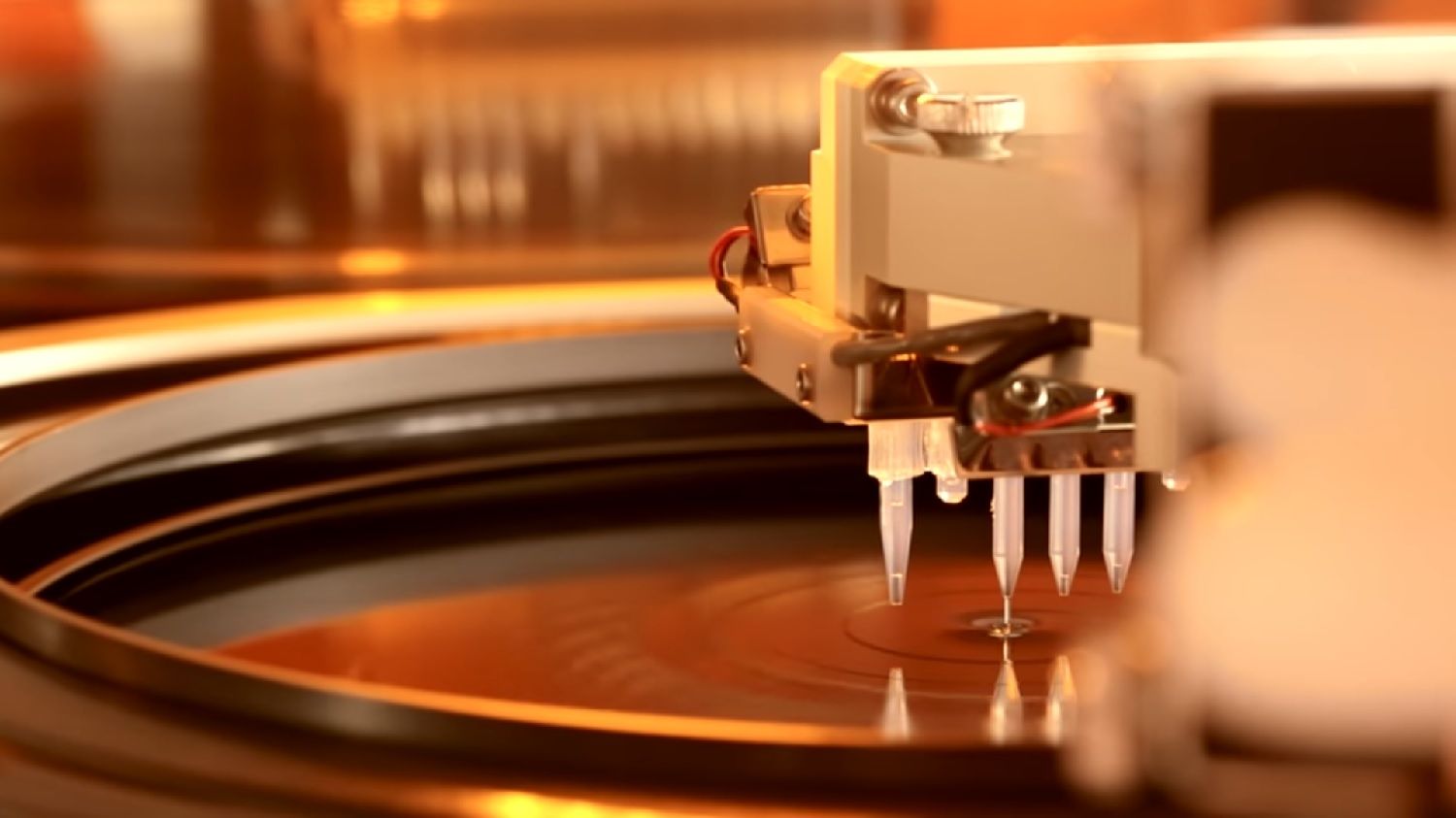
Étape 3 : La résine photosensible
Ensuite, le wafer est uniformément recouvert de manière épaisse, sensible à la lumière appelée résine photosensible. Certaines parties du wafer sont sélectionnées pour être exposées en alignant soigneusement un masque entre une source de lumière ultraviolette et le wafer. Dans les zones ajourées du masque, la lumière passe et atteint la résine. Lorsqu’elle est exposée à une lumière ultraviolette, la résine photosensible subit un changement chimique, qui permet à un liquide développeur de retirer la résine exposée et de laisser celle non exposée sur le wafer. Le processus de photolithographie/résine photosensible est répété pour chaque masque requis par le circuit.
Étape 4 : La gravure
Au cours de l’étape de gravure, un plasma est appliqué sur le wafer pour creuser les parties de la couche de nitrure qui ne sont pas protégées par la résine photorésistante. Cette opération laisse sur le wafer un motif correspondant exactement à celui du masque. Une fois la résine retirée (nettoyée) à l’aide d’un autre produit chimique, des centaines de puces de mémoire peuvent être gravées sur le wafer.
Partie II : Stratification et finalisation du circuit
Dans la Partie I du processus de fabrication, tous les éléments du circuit (transistors, résistances et condensateurs) ont été créés avec le premier masque. Les prochaines étapes consistent à connecter ces éléments entre eux en créant un ensemble de couches.
Étape 5 : La couche d’aluminium
Pour commencer à connecter entre eux les éléments du circuit, une couche de verre au borophosphosilicate (BPSG) isolante est déposée sur le wafer, puis un masque de contact est utilisé pour définir les points de contact (ou fenêtres) de chaque élément du circuit. Une fois les fenêtres de contact gravées, l’intégralité du wafer est recouverte d’une fine couche d’aluminium dans une chambre de pulvérisation. Lorsqu’un masque de métal est appliqué à la couche d’aluminium, un réseau de minuscules fils en métal se forme, créant ainsi une connexion pour le circuit.
Étape 6 : Couche de passivation
L’intégralité du wafer est ensuite recouverte d’une couche isolante de verre et de nitrure de silicium pour le protéger de toute contamination au cours de l’assemblage. Ce revêtement protecteur est appelé « couche de passivation ». Un processus final de masquage et de gravure de la couche de passivation s’ensuit afin d’excaver la couche isolante au niveau des terminaux, les pattes de liaison. Ces pattes de liaison à présent à l’air libre seront utilisées pour connecter électriquement le « die » à des broches en métal sur le packaging en plastique ou en céramique. Le circuit intégré est à présent complet. Avant que le wafer soit envoyé pour l’assemblage du « die », chaque circuit intégré du wafer est testé. Les puces fonctionnelles et défectueuses sont toutes identifiées et répertoriées dans un fichier informatique. Une scie à lame diamantée vient ensuite découper le wafer en puces individuelles. Les puces défectueuses sont éliminées, tandis que les autres sont prêtes pour l’assemblage. Ces puces individuelles sont appelées « die ». Avant d’être encapsulés, ils sont montés sur des cades de plomb où de fins fils d’or viennent relier les pattes de liaison des puces aux cades pour créer un chemin électrique entre le die et les pattes en plomb.
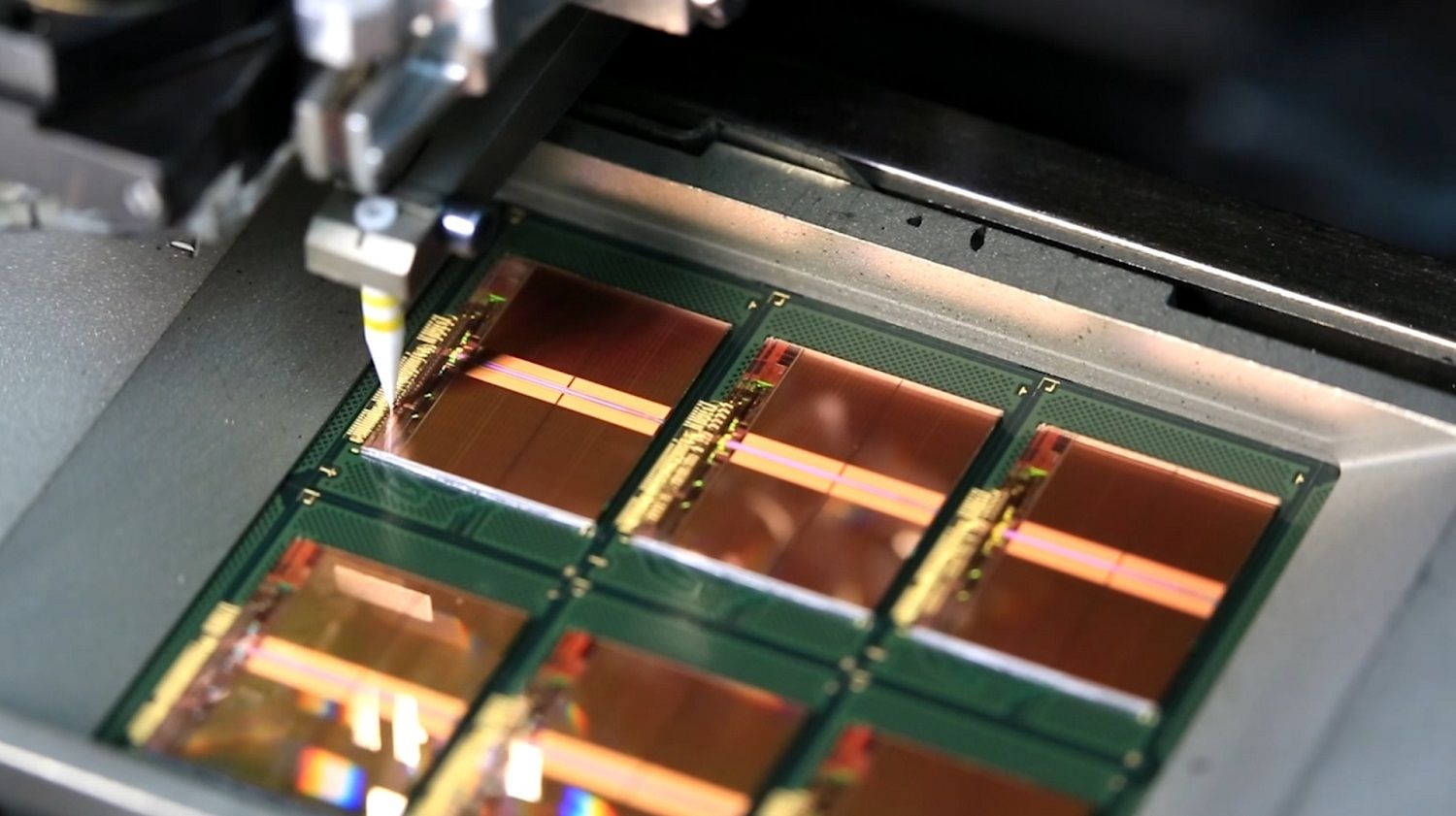
Partie III : Préparation et test du « die »
Au cours de la Partie II du processus de fabrication, le circuit intégré a été créé et le wafer fini a été découpé en plusieurs « dies ». Les prochaines étapes consistent à préparer le « die » pour qu’il puisse être utilisé dans un module fini.
Étape 7 : L’encapsulation
Au cours de l’encapsulation, les cadres en plomb sont placés sur des plaques de moulage puis chauffés. Le plastique fondu est pressé autour de chaque die pour former son package individuel. Le moule est ouvert, les cadres en plomb sont ensuite retirés puis nettoyés.
Étape 8 : La galvanoplastie
La galvanoplastie est la prochaine étape du processus au cours de laquelle les cadres en plomb sont "chargés électriquement" en les plongeant dans une solution d’étain et de plomb. Ici, les ions de l’étain et du plomb sont attirés par le cadre en plomb chargé électriquement, créant ainsi un dépôt uniforme plaqué, améliorant la conductivité du « die » et offrant une surface lisse pour que celui-ci puisse être monté.
Étape 9 : Découpe et formage
Lors de la découpe et du formage, les cadres en plomb sont placés dans des machines qui forment les pattes puis détachent les puces des cadres. Les puces sont ensuite placées dans des tubes antistatiques pour pouvoir être manipulées puis transportées vers la zone de test où elles subiront les derniers contrôles.
Étape 10 : Le déverminage
Au cours de l’étape de déverminage, chaque puce est testée pour voir comment elle fonctionne en conditions d’utilisation intensive. Cette opération est critique pour la fiabilité des modules. En testant les modules en conditions d’utilisation intensive, nous sommes en mesure de repérer les quelques modules de chaque série qui tomberont en panne après une courte utilisation. Pour ce faire, nous utilisons des fours AMBYX révolutionnaires que nos ingénieurs ont spécialement développés pour le déverminage de nos puces. Une fois que les puces de mémoire ont passé l’étape de déverminage, elles sont inspectées, scellées, et prêtes à être assemblées.
Étape 11 : Assemblage et fabrication du circuit imprimé
Une fois les puces de mémoire fabriquées, elles doivent être connectées à la carte mère de votre ordinateur. Les circuits imprimés permettent de résoudre ce problème en fournissant une interface de connexion entre les puces et la carte mère. Pour procéder ainsi, les puces sont montées sur un circuit imprimé pour constituer un module de mémoire fini. Les circuits imprimés comportent plusieurs circuits identiques juxtaposés sur la même planche. Une fois l’assemblage terminé, la planche est découpée en modules individuels, comme on découperait une tablette de chocolat en plusieurs carrés. En modifiant le nombre total circuits imprimés sur chaque planche en fonction de leur taille, Micron arrive à maximiser le nombre de modules fabriqués à partir d’une quantité de matières premières donnée.
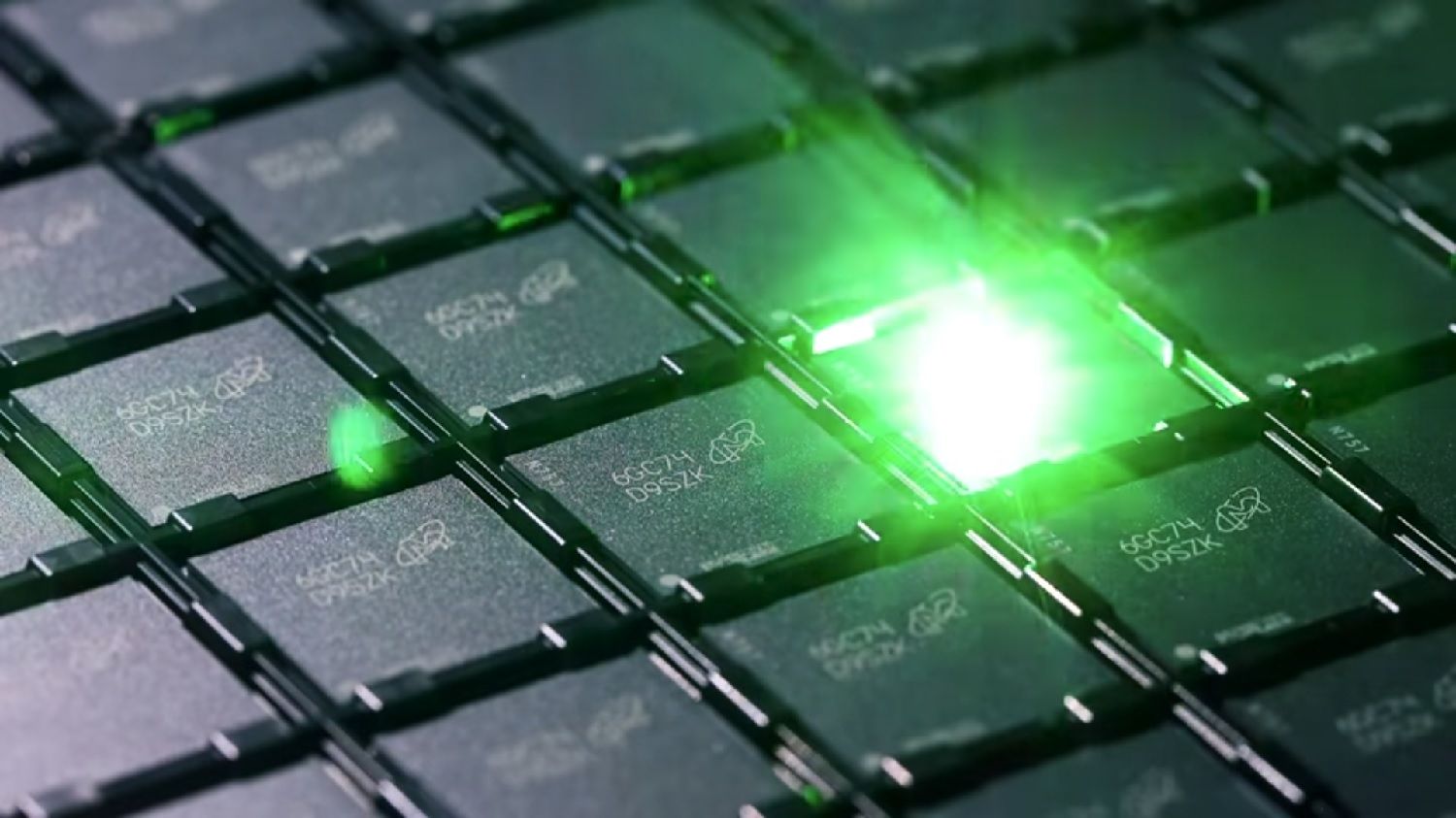
Partie IV : L’assemblage du module
Dans la Partie III du processus de fabrication, le « die » et le circuit imprimé ont été préparés pour l'assemblage final du module. Les dernières étapes correspondent au processus d'assemblage du module.
Étape 12 : La sérigraphie
Une fois la conception du module parfaite et les circuits imprimés fabriqués, l’assemblage du module de mémoire commence. L’assemblage implique une procédure de soudure complexe qui permet de fixer les puces de mémoire au circuit imprimé. La sérigraphie est la première étape de cette procédure. On utilise alors un pochoir pour appliquer une crème à braser sur le circuit imprimé fini. La crème à braser est une substance collante qui maintient les puces en place sur le circuit imprimé. L’utilisation d’un pochoir permet de s’assurer que la crème à braser ne sera appliquée qu’aux endroits où les composants (puces) viendront se fixer. Les points d’attache sont simples à trouver, grâce à des repères sur le circuit imprimé qui indiquent où les puces doivent être placées. Une fois la crème à braser appliquée, des machines transfert automatisées scannent les repères afin de déterminer où positionner les puces sur le circuit imprimé. Les machines transfert sont programmées pour savoir quelles puces sont placées à quel endroit. Lorsque l’une d’elles saisit une puce dans le chargeur et la place sur le circuit imprimé, elle sait exactement où le faire. Le processus de placement des puces a lieu pour toutes les autres puces et composants du module. De toutes les étapes de la fabrication de la mémoire, celle-ci est la plus rapide : les puces sont placées sur le circuit imprimé en quelques secondes.
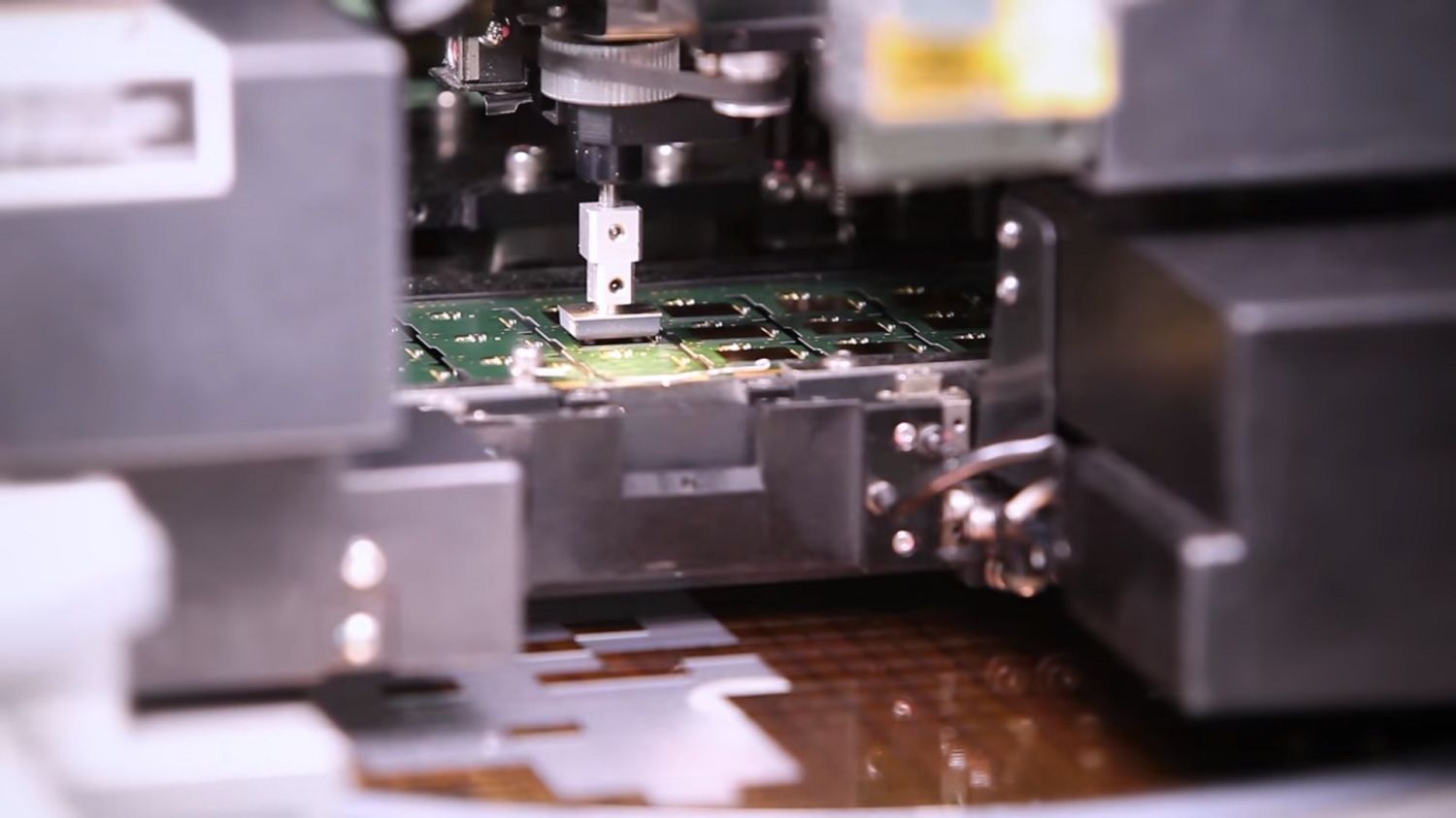
Étape 13 : La soudure et la connexion
Ensuite, les puces et circuits assemblés passent dans un four. La chaleur de celui-ci fait fondre la crème à braser qui devient alors liquide. Lorsqu’elle refroidit, elle se solidifie, créant des connexions permanentes entre les puces de mémoire et le circuit imprimé. La tension superficielle de la crème fondue empêche les puces de se décaler au cours du processus. Une fois les puces fixées, la planche est découpée en modules individuels. Les membres des équipes Micron inspectent ensuite chaque module. De nombreux modules subissent ensuite des vérifications supplémentaires au moyen de machines à rayon X automatiques qui permettent de s’assurer que les connexions ont été correctement soudées. Tous les modules de mémoire Micron sont conformes aux critères de la norme IPC-A-610, la plus répandue dans le secteur.
Étape 14 : Le contrôle qualité post-assemblage
Micron teste et étiquette alors les modules. Nous utilisons du matériel propriétaire pour tester automatiquement les performances et le bon fonctionnement de chaque pièce. Ce dispositif permet d’éviter qu’un opérateur place par erreur un module défaillant avec ceux qui ont réussi le test. Certains modules intègrent une "« plaque d’identité »" que votre PC reconnaît et lit.
Étape 15 : L’expédition
Avant d’être envoyés aux fabricants d’ordinateurs et aux clients, une importante quantité de produits finis sont sélectionnés au hasard pour une inspection finale. Une fois qu’ils sont approuvés, ils sont placés dans des emballages antistatiques puis sont préparés pour l’expédition. Une fois ce long processus de fabrication terminé, votre mémoire est prête à l’emploi. Elle a été rigoureusement testée et approuvée. Pour en apprendre plus sur les unités de mémoire, cliquez ici.
©2018 Micron Technology, Inc. Tous droits réservés. Les caractéristiques techniques, informations et/ou produits contenus dans ce document peuvent être modifiés sans préavis. Crucial et Micron Technology, Inc. ne sauraient être tenus pour responsables de toute omission ou erreur figurant dans la typographie ou les photographies. Micron, le logo Micron, Crucial et le logo Crucial sont des marques déposées ou de commerce de Micron Technology, Inc. Toutes les autres marques de commerce et marques de service sont la propriété de leurs détenteurs respectifs.